Blog /
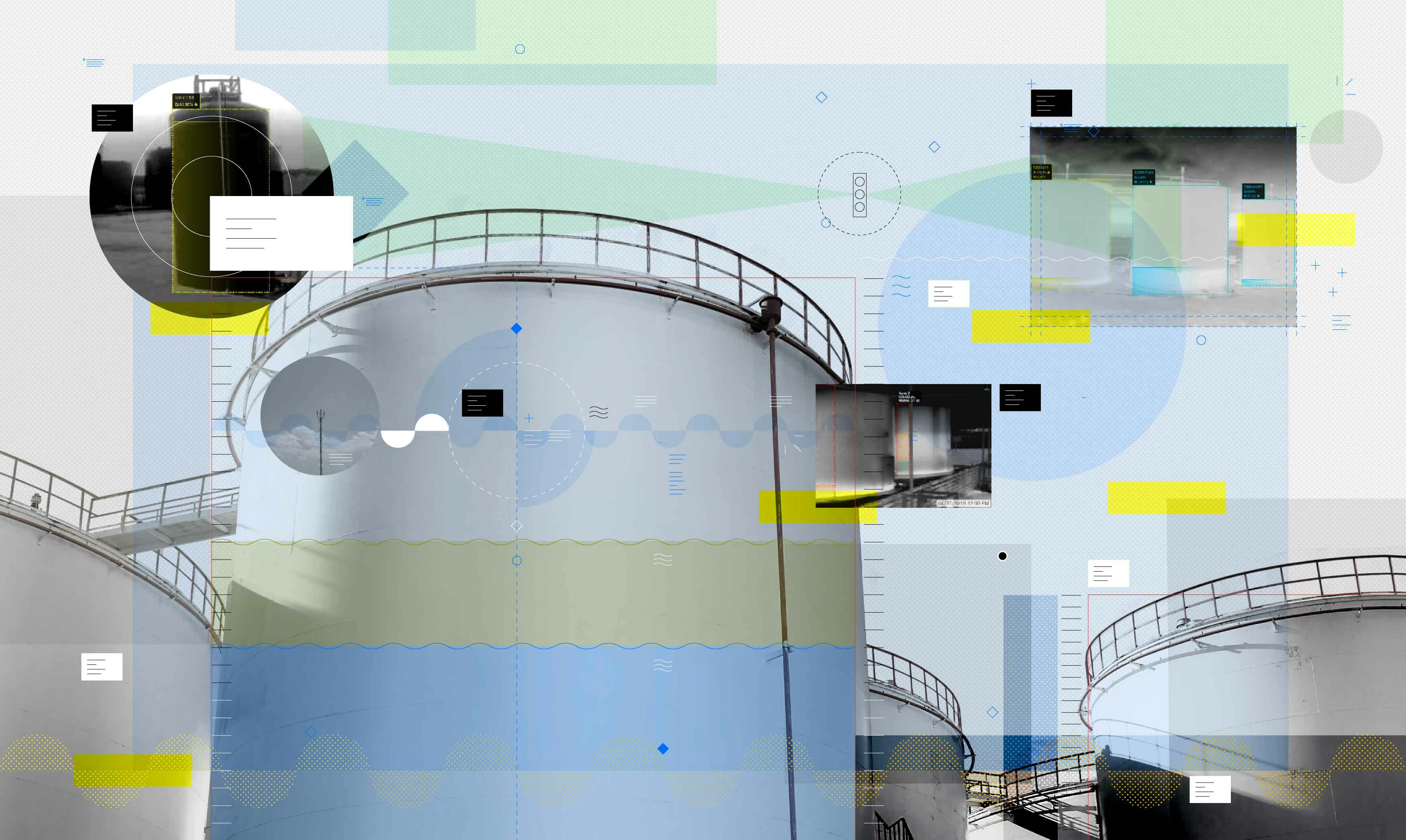
Efficiently Monitoring Tank Levels: A Guide for Oil and Gas Operators
The Evolution of Tank Monitoring
From traditional manual tank gauging to the sophisticated infrared imaging, the industry has seen a remarkable transformation in tank level monitoring strategies:
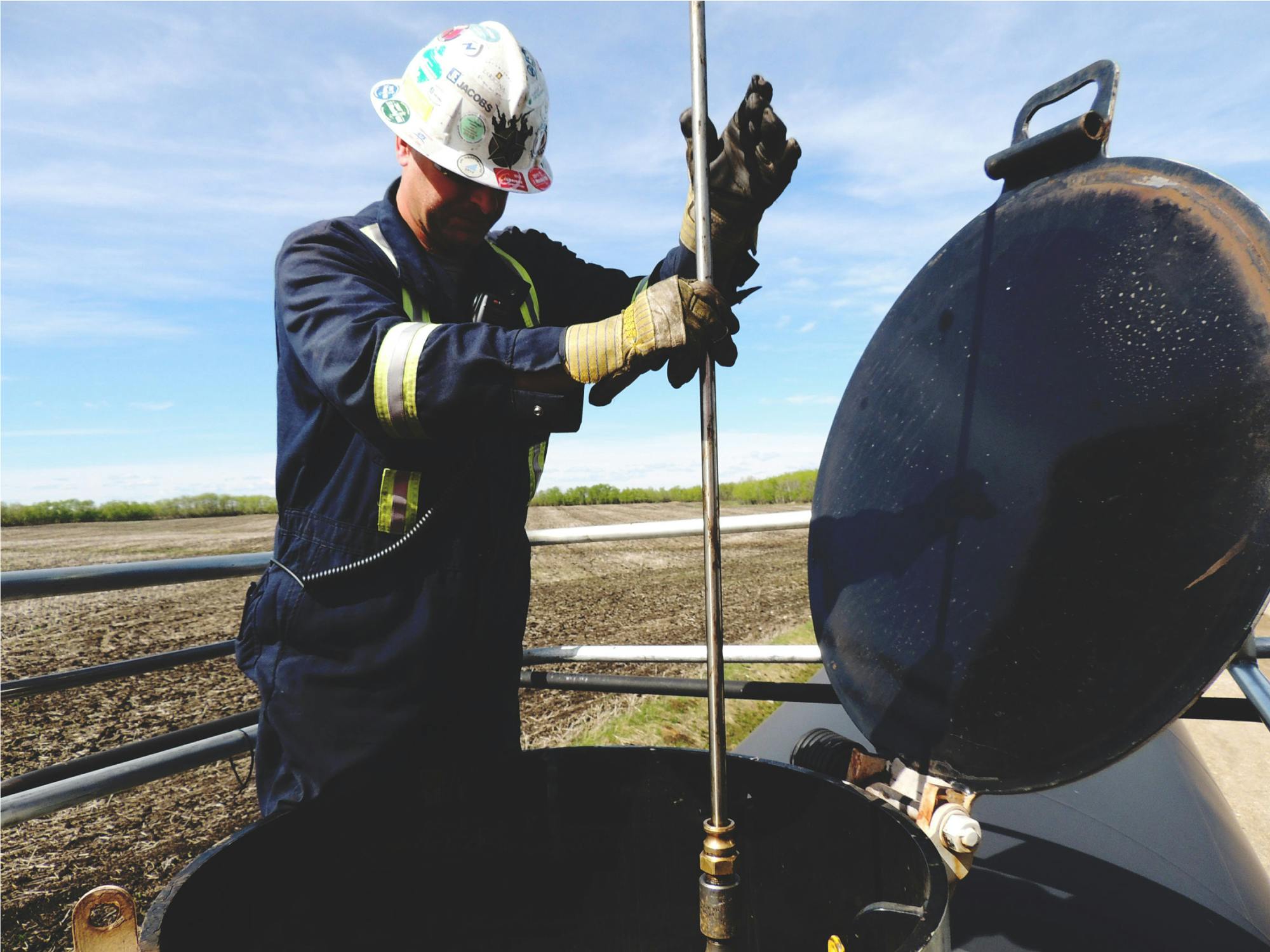
1. Manual Tank Gauging:
Historically, manual tank gauging stood as the cornerstone for assessing when a storage tank reached its full capacity. Even today, this method remains prevalent among oil and gas companies regardless of its size.
However, the manual tank gauging harbors intrinsic challenges when managing numerous or remote oil pads, notably including human error, and potential security issues such as oil theft.
Pros:
- Low Initial Costs: It doesn't require a substantial investment in advanced technology.
- Simple to Implement: It can be easily implemented without needing sophisticated tools.
- Independence from Power Sources: As it doesn’t rely on electrical systems, there's no risk of failure due to power outages.
- Suitability for Small Operations: For smaller operations with a limited number of tanks, manual gauging can be sufficient.
- No Technical Glitches: It is free from technical malfunctions that can sometimes plague electronic monitoring systems.
Cons:
- Safety Concerns: It can be a dangerous process due to the potential exposure to hazardous chemicals and the risk of falls or other accidents.
- Human Error: Being a manual process, it is prone to errors, which can result in inaccurate readings.
- Time-Consuming: It is labor-intensive and takes a lot of time, especially for operations with a large number of tanks.
- Inefficiency: For large operations, manual tank gauging is not the most efficient method, leading to a slower response time in addressing issues.
- Health Hazards: Regular exposure to volatile organic compounds (VOCs) can pose serious health risks to the workers.
- Security Issues: The method is more susceptible to fraudulent reporting and theft as it depends on individual reporting.
- Limited Data Analysis: It does not allow for the detailed data analysis and reporting that automated systems can provide, which can help in optimizing operations.
- Environmental Concerns: Incorrect readings can potentially lead to overflows, causing environmental damage.
- Compliance: Opening tank hatches in specific regions can result in substantial fines.
While manual tank gauging might still find utility in smaller, less complex operations, it is clear that for large-scale operations, more advanced, automated systems would offer greater benefits, ensuring safety, accuracy, and efficiency
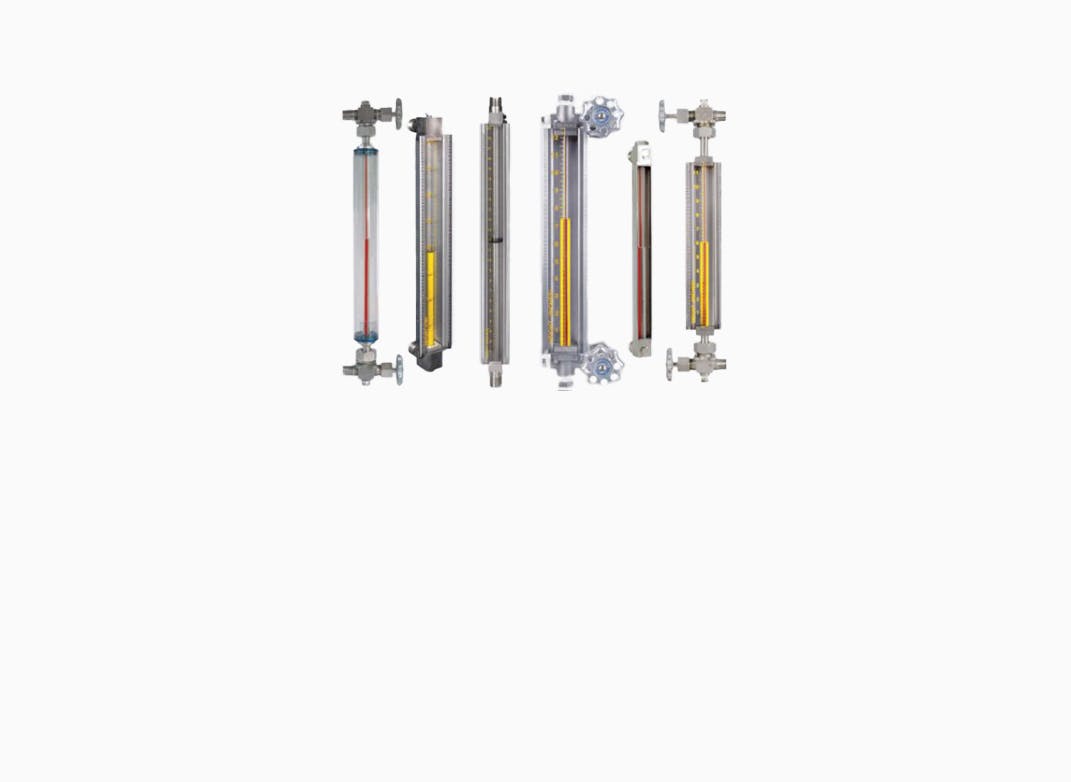
2. Sight Glass:
Similarly, sight glasses, or small windows integrated into storage tanks, afford personnel the ability to view tank levels without opening the hatch. While convenient for day-to-day monitoring for onsite personnel, they present limitations such as staining and restricted visibility that fails to account for sludge build-up.
Pros:
- Simplicity and Ease of Use: A sight glass is straightforward to use, requiring no technical knowledge to interpret the readings.
- Cost-Effective: Compared to more advanced monitoring systems, installing a sight glass is generally more cost-effective.
- Real-Time Monitoring: It allows for real-time visual monitoring of the tank contents, which can be especially useful in routine operations.
- Reduced Need for Manual Gauging: By providing visual insight into the tank, it reduces the frequency of manual gauging, saving time and reducing risk.
Cons:
- Limited Visibility: The sight glass offers limited visibility into the tank, unable to provide comprehensive information about conditions inside the tank, such as sludge buildup.
- Maintenance: Sight glasses can stain and require regular cleaning to remain effective.
- Safety Risks: If not maintained properly, sight glasses can break, posing a safety risk and potentially leading to leaks.
- Manual Monitoring: It still necessitates personnel to physically check the levels, which can be time-consuming in large facilities.
- Inaccuracy: The sight glass might not always give accurate readings, especially if there are issues like bubbles or foam in the liquid.
- Not Suitable for Remote Locations: For tanks located in remote areas, the need for a person to be present to read the sight glass makes this method less practical.
- Environmental Conditions: Factors like lighting conditions and weather can affect the visibility and accuracy of readings through a sight glass.
While sight glasses offer a simple and affordable solution for monitoring tank levels, they may not be suitable for all operations, especially large-scale and remote operations where more automated and accurate systems are required. It can serve well in controlled environments with regular maintenance and where human monitoring is feasible.
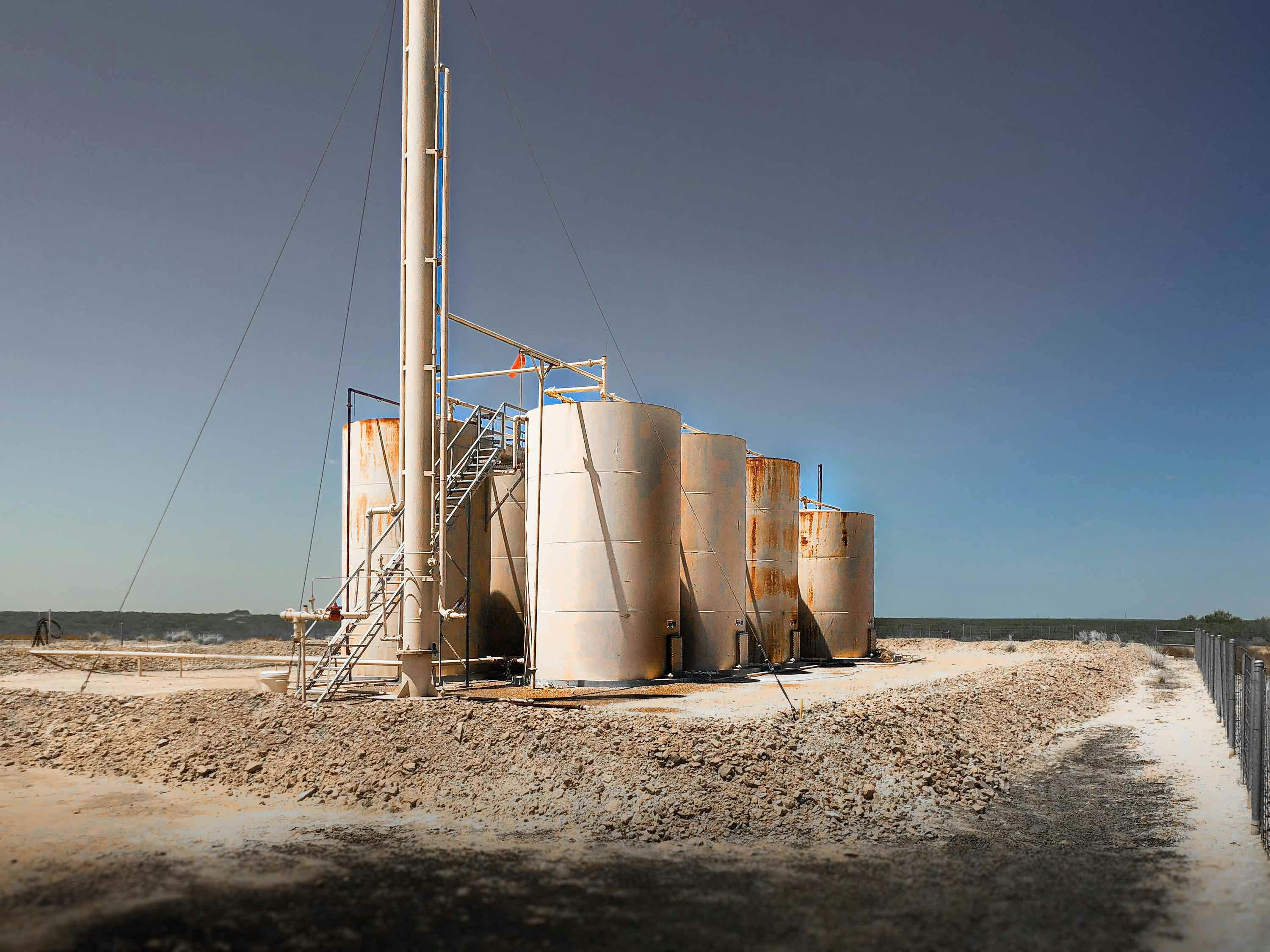
3. Stepping into Automation with Guided Wave Radar
The Guided Wave Radar technology heralds a shift towards automated monitoring, liberating operators from the necessity of on-site personnel to check fluid levels. This technology effectively monitors storage tanks, transmitting the vital data directly to the operators.
Despite the considerable advancements it offers, the technology is not devoid of drawbacks including high installation costs, susceptibility to sludge build-up, and the occasional false alarms that necessitate a revert to manual gauging.
Pros:
- Automation: GWR allows for automated monitoring, which can save time and reduce labor costs.
- Accuracy: It generally provides highly accurate measurements, enhancing the efficiency of tank management.
- Real-Time Data: Operators can receive real-time data, allowing for quick responses to any changes in tank levels.
- Safe: This method is non-contact, meaning it can safely be used in tanks containing hazardous materials.
- Compatibility with Various Liquids: GWR can be used to measure the levels of a wide variety of liquids, making it a versatile choice for different applications.
- Remote Monitoring: Facilitates remote monitoring, reducing the necessity for personnel to be on-site and potentially in hazardous environments.
Cons:
- Cost: Installing GWR systems can be expensive, particularly when retrofitting existing tanks.
- Maintenance: Over time, the buildup of sludge and other materials on the sensor can affect its performance, necessitating regular maintenance.
- Complex Installation: The installation process can be more complex compared to simpler systems, potentially requiring expert knowledge and experience.
- False Alarms: The radar system can sometimes trigger false alarms, which can disrupt operations and require additional resources to address.
- Intrusive: Since devices are installed inside the tanks, they can be considered intrusive, and installation might necessitate tank downtime.
- Potential for Malfunction: Like all technology, GWR systems can malfunction, possibly leading to inaccurate readings and the requirement for manual intervention.
- Calibration: The system needs to be correctly calibrated for the specific liquid being measured to ensure accurate readings, which can be a complex process.
While guided wave radars bring a high degree of accuracy and automation to the monitoring of tank levels, they come with higher costs and maintenance requirements.
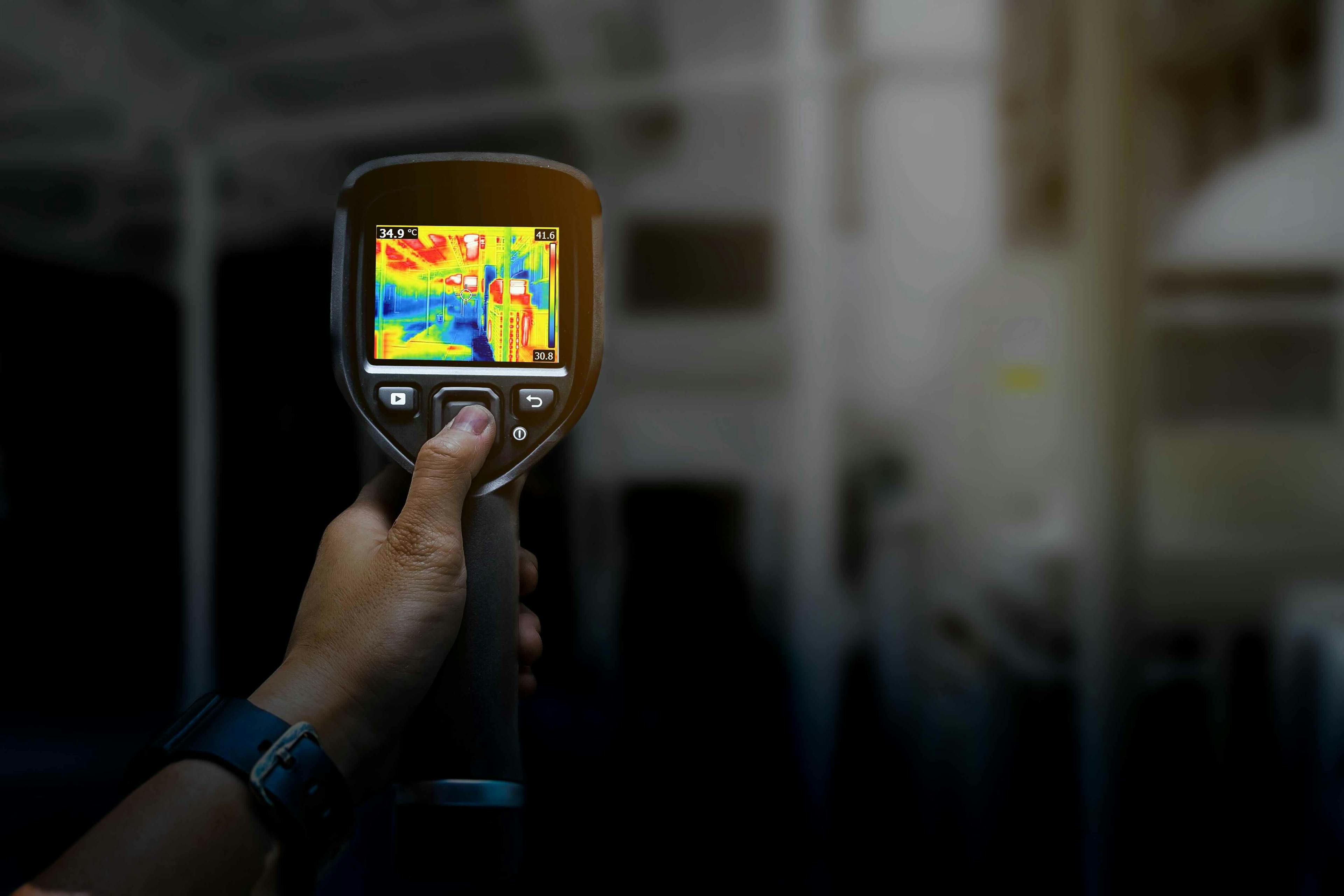
4. A Leap into the Future: Infrared Monitoring
The latest in the line of monitoring technologies is the infrared monitoring system, where devices, installed externally, enable operators to visualize the contents of their tanks, distinguishing clearly between water and oil. This autonomous system stands as a testimony to the merger of efficiency and technology, eliminating concerns over sludge build-up and manual cleaning.
The Andium Advantage
At the forefront of this innovation is Andium, elevating tank monitoring with a fusion of infrared technology and groundbreaking automation. The Andium system stands apart, offering the capabilities of monitoring multiple storage tanks at the fraction of the cost of a single Guided Wave Radar.
Our system keeps you aware of tank levels, sending timely alerts to prevent overflows and ensuring transparency before haulers arrive, mitigating risks of short loads.
- Cost-Effectiveness: Monitor multiple tanks with one device
- Alert Systems: Automated alerts for rising tank levels to prevent overflows.
- Real-time Data: View tank levels before a hauler arrives, ensuring accurate loads.
- Convenience: With Andium technology monitoring your locations, operators can prioritize other critical operational tasks.
- User-Friendly Interface: Accessible through a mobile-friendly dashboard, Andium also offers keyword searches for specific events across all locations.
Why leading energy companies choose Andium
Choosing Andium is synonymous with embracing efficiency and reliability. Our solutions are trusted globally by leading oil and gas companies, aiding in maintaining compliance and optimizing costs.
Andium stands ready to assist you in leveraging technology to enhance your operational efficiency, providing vital insights for improved decision-making in critical situations. We invite you to experience the Andium advantage. Contact us through the form below and embark on a journey towards unparalleled efficiency in tank monitoring with Andium.
Get a Quote
Reach out for more information and we’ll be in touch soon.